Mobile: 8613421351153
Sandwich panel
Classification of sandwich panel by function
Classification of sandwich panels by core material
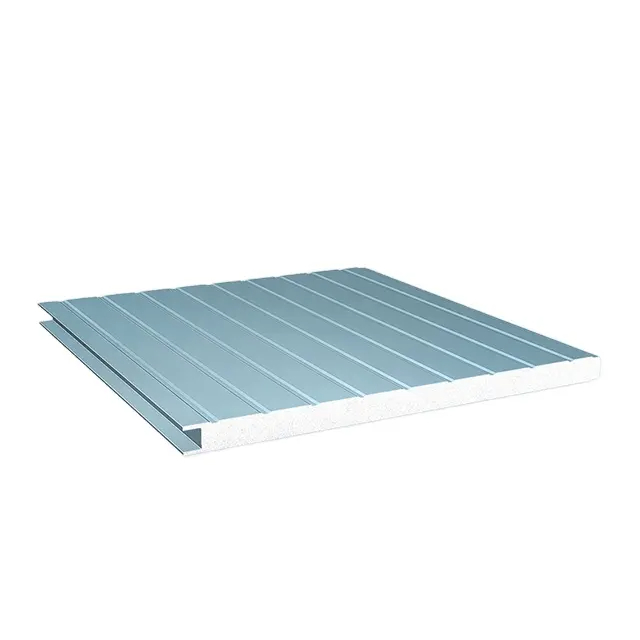
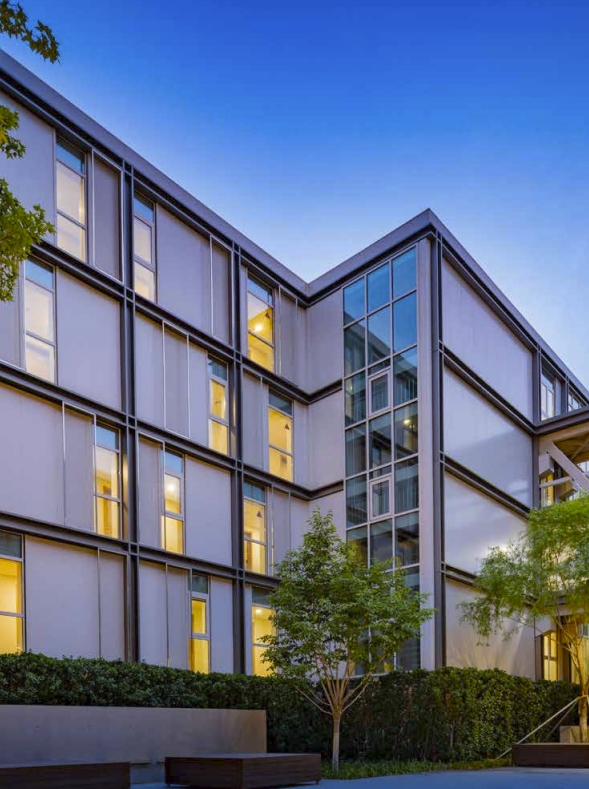
What is the sandwich panel
Sandwich panel, also known as composite panels or structural insulated panel, is a type of multi-layer structural cladding system that consists of two thin and strong metal sheets attached to a substantiating core material. The metal sheets are coated with a corrosion-resistant coating and the core material is usually polystyrene, polyurethane, mineral wool.
The structural functionality of a sandwich panel is similar to the classic I-beam, where two face sheets primarily resist the in-plane and lateral bending loads (similar to flanges of an I- beam), while the core material mainly resists the shear loads (similar to the web of an I-beam).[1] The idea is to use a light/soft but thick layer for the core and strong but thin layers for face sheets. This results in increasing the overall thickness of the panel, which often improves the structural attributes, like bending stiffness, and maintain or even reduce the weight.
In building and construction, these prefabricated products designed for use as building envelopes. They appear in industrial and office buildings, in clean and cold rooms and also in private houses, whether renovation or new-build. They combine a high-quality product with high flexibility regarding design. They generally have a good energy-efficiency and sustainability.